New dyeing and finishing innovations have traditionally been kept under wraps until being launched with a fanfare at a show – sometimes it has been evolution, for example the trend to lower liquor ratio dyeing machines, and sometimes it has been more revolutionary, such as the rapid of digital inkjet printing for textiles. However, there is now no timetable for innovation in textile dyeing as the industry moves rapidly towards a more sustainable future.
Some textile machinery companies have recently introduced brand new commercial options for concepts such as CO2 dyeing (Dyecoo) and others have looked recently at improvements in the cationised dyeing process, but most have focused on launching new textile machines that can be retrofitted into existing textile dye house set-ups.
The 1990’s saw the emergence of innovations to improve textile quality such as low lift, soft-flow dyeing machines and also major developments on control systems to ensure dyeing processes were carried out more consistently than ever before.
The introduction of sophisticated systems for dosing chemicals with great accuracy, heating and cooling machines to within a fraction of a degree of a pre-programmed profile and control of specific gravity and pH, enabled textile dyers to achieve unprecedented levels of right-first-time dyeing.
The need for good dye and chemical storage and accurate dispensing also saw a large rise in the number of systems available to the dyer and printer, ranging from high-cost fully automated machines to lower cost check-weigh apparatus.
Drying machines such as relax driers and stenters were also supplied with an array of control systems to allow the finisher to confidently manage bow, skew, weight, width, moisture levels and fabric ‘basics’ to previously unachievable levels of consistency. The improved controls and development of customisable pad mangles also enabled finishers to apply and cure resins and performance finishes with hitherto unimaginable levels of confidence.
Fabric finishing moved from relatively simple methods of drying fabric to interesting, innovative methods of surface modification – companies such as Lafer and Mario Crosta led the way with a range of brushing and sueding machines, Biancalani developed fabric tumblers and, as technical textiles became more prominent, coating and lamination machines became more mainstream.
The main driving forces for most of the pre-2000 developments were better quality, better consistency, lower cost production and the need for new, innovative products. The aim of the machinery manufacturers was largely to enable dyers to make more product, more consistently and more profitably – and their marketing reflected this.
Of course all the developments to reduce water, energy and chemical use had benefits for the environment but ‘The Environment’ didn’t really become an issue in its own right until the turn of the century, since when it has been THE big story in the dyeing and finishing industry.
Recent technology developments
The last two ITMA shows have been dominated by developments and innovations that could be marketed as being ‘green’ – and the great thing about the dyeing and finishing industry is that virtually everything that has a lower environmental impact will have a lower cost for the dyer.
The need for lower cost and lower environmental impacts has never been greater – as the downward pressure on retail prices for textiles continues we are seeing increases in energy, water, fibre and chemical costs, and the net result is that dyers, printers and finishers are being squeezed as never before.
So, while textile machinery manufacturers and dye and chemical companies may be dressing everything up as ‘green’ or ‘environmentally friendly’ developments, the brutal truth is that the industry has no option but to invest in low impact manufacturing if it is to survive.
As legislation and policing on pollution become tighter it is more difficult for those dyers to cut corners by under-hand measures such as discharging untreated effluent or failing to manage air emissions and waste. Resorting to cheap dyes and chemicals has often been the route of choice for dyers wishing to cut corners, but in most cases the cheapest raw materials are shown to be a false economy with the cost of failure far outweighing the savings.
For many observers, the recent ITMA 2015 in November was the ‘greenest’ show yet and the latest trend appears to be an effort to quantify the reduction of environmental impacts and present them in terms that can be understood (and promoted) by large retail brands.
In addition to messages aimed at dyers in old style litres per kilogram terms we saw more use of carbon and water footprints in an attempt to de-mystify textile dyeing and get the vast improvements we’ve seen over the past couple of decades judged alongside other less impressive but more newsworthy environmental initiatives.
The other challenge that dyeing machinery manufacturers and dye and chemical suppliers have is that the baseline is constantly changing so cynics can rightfully ask what the quoted savings are based on – is it industry average, the last model of machine or the figures for 1970?
But we shouldn’t get too bogged down with mathematics – the leaders in the industry are improving and there are some interesting themes emerging.
Green peripherals
The integration of ‘green’ add-ons and peripherals into core machinery design has become more popular with optional extras such as heat recovery units being built in at source rather than retro-fitted, and out-of-box solutions for ancillary processes have become more widely available rather than dyehouse owners relying on in-house engineers to create bespoke solutions.
A good example of the latter is Fongs water re-use systems where manufacturers get a trusted name from industry to manage a zero-discharge effluent and water re-cycling system. Of course it isn’t quite as simple as plug and play but the big, reputable brands are waking up to the fact that there are opportunities beyond basic machinery sales.
Swiss-based Benninger has taken energy efficient continuous washing to another level with its established integrated heat recovery systems and counter-flow wash technology – and insulated wash boxes. Gone are the days when continuous washing was the least efficient way to wash dyed fabrics and we can see a time when batch-dyeing machines are used for dyeing only, with the washing being done on dedicated ultra-efficient ranges. The company recently unveiled the new ‘Tempacta’ washing steamer which has been developed for all low tension washing processes and is mainly used for diffusion washing (fastness washing) and for the relaxation of knitwear. As a washing drum can be integrated, an intermediate rinsing process or additional intensification of washing is also possible.
Jet dyeing machines continue to evolve and improve with the focus on reduced water and energy consumption. Thies displayed an ‘optimised’ version of its iMaster H2O with in-kier winch reel – which gives a smoother fabric passage at lower liquor ratios. On the garment dyeing side Italian firm Tonello can now take liquor ratios down to lows of 2:1 using a spray technique, but nothing gets a low as Cold Pad Batch and the likes of Erbatech can still expect good sales as textile dyers embrace the low impact, low cost and, increasingly, low risk opportunities of new tightly controlled CPB systems to reduce carbon footprints by 60 per cent when compared to jet dyeing.
Dispensing advice
In addition to greater levels of control, the dispensing companies are also moving towards lower volumes and therefore lower volumes of waste – particularly the print dispensing systems where waste accounts for a significant cost and effluent loading.
The dye and chemicals companies will be promoting their health safety and environmental credentials and we can expect more new information on existing products rather than new products. As brands and consumers become more aware of potential issues with hazardous chemicals, reputable companies are actively promoting products that are free from certain chemicals such as in the DWR fabric sector where PFC (perfluorocarbon) free products are being developed due to problematic by-products such as the bio-persistent PFOA which has become heavily restricted.
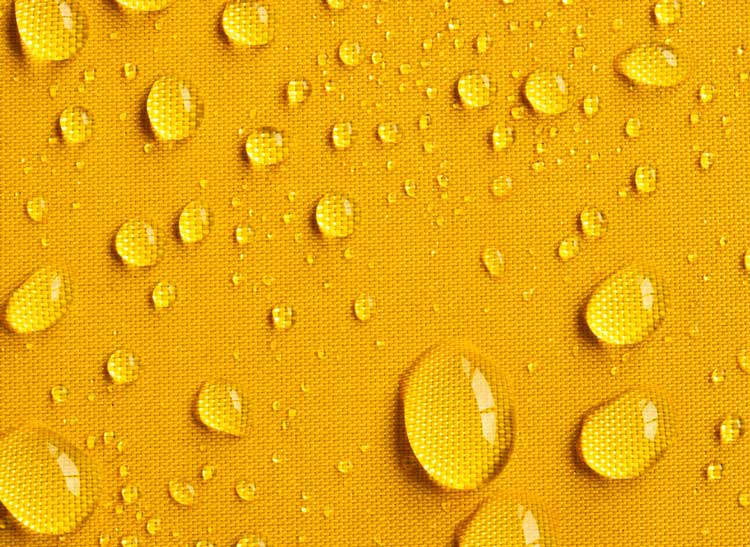
DyStar has completed a life cycle analysis on its own processes and this information is available alongside the product specific health, safety and environmental information we have come to expect from them.
However it’s clear that new products and the growing trend in the use of plant-based raw materials will feature heavily in the industry going forward. Archroma is already promoting its Earthcolor range of dyes synthesized from leaves and the non-edible shells of nuts.
Elsewhere, enzymes are known to help dyers lower the temperature, and therefore energy requirement of processes such as bleaching but some chemicals are already on the market from companies such as CHT that can reduce the temperature of cotton bleaching by up to 30oC.
As far as dyes are concerned there will be very little revolutionary change but dyers should embrace ‘rapid evolution’ such as the Avitera SE reactive dyes from Huntsman that give over 90 per cent dye fixation and therefore require shorter, cheaper, lower impact wash off processes than previous generations.
All in all 2016 promises to offer huge opportunities for textile dyers and finishers to reduce their processing costs by reducing water, energy and chemical consumption but it remains to be seen if the industry is prepared to invest. In addition to new machinery and chemicals we may also need to look at new business models, such as leasing, to get the latest brilliant developments out of the showrooms and into the more textile factories as part of a new more sustainable business model.
Intro Image of denim: Image: © jasburn | iStock